How does a blocked DPF damage the turbo?
Fitted to diesel vehicles from 2009, the diesel particulate filter, or DPF for short, is designed to stop soot, and other harmful particles produced during the combustion cycle, from exiting the exhaust. The trapped soot must then be periodically emptied or ‘burned off’ through regeneration.
Yet just like any other filer filter they can easily become blocked and obstruct the flow of gas through the exhaust system. If the gas cannot be expelled from the engine quickly enough, it will start to build up, creating back pressure. And as the pressure increases, so does the temperature of the gas in and around the turbo’s turbine housing. Whilst this may only cause problems such as oils leaks and coking initially, if left unchecked, the turbo can very quickly fail, or the ECU may put the vehicle into limp mode. Either way your customer is liable for an expensive repair bill.
What causes a blocked DPF?
There are several factors that can cause the DPF to block prematurely and/or stop DPF regeneration from working effectively, or even starting. These include:
- frequent stop-start or short journeys at low speeds, where the engine fails to reach the optimum temperature for regeneration
- a dashboard warning light or a diagnostic trouble code stored in the ECU can also prevent regeneration.
- sulphated ash and/or additives contained in some oils can block the filter prematurely – to prevent build-up a low ash, low sulphur engine oil should always be used.
- a faulty fuel injector or turbocharger can cause the vehicle to run rich creating excessive soot. Similarly, a faulty EGR valve can increase the production of diesel particulates, both causing the DPF to become blocked quicker than normal.
- many vehicles will not initiate an active regeneration if the fuel or Eolys™ additive tank is less than a quarter full.
- the DPF on a poorly service vehicle may fail sooner since factors such as oil quality and level can also prevent regeneration.
What are the signs of turbo damage due to a blocked DPF?
The following signs are good indicators of a DPF related issue. The amount of damage this will cause largely depends on how much the DPF is restricting the flow of exhaust gas.
- fault code triggered – this may include exhaust pressure control, EGR, DPF regeneration and/or turbo boost control related codes
- DPF warning light illuminated
- in severe cases it may cause the vehicle to go into limp-home mode, limiting it to certain speeds or revs, to protect it from further damage
- reduced turbo efficiency given the exhaust’s inability to remove gas from the engine.
- discolouration of parts within the CHRA due to heat transfer – whilst this is typical of other issues, mainly oil starvation, the pattern will help streamline your diagnosis. Discolouration that starts at the turbine wheel and continues through the shaft to the compressor side is a clear signal of excessive temperatures caused by rising back pressure
- oil leaks can occur when the rising back pressure forces the exhaust gas past the shaft seal on the turbine side, and into the CHRA, displacing the oil, and pushing it through the seals on the compressor side

- the additional back pressure can also push exhaust gas through the small clearances in the wastegate, creating a build-up of carbon in and around the wastegate and its control mechanisms. If bad enough, the wastegate door can stick in the open or closed positions and the ECU will no longer be able to control boost pressure.
- excessive temperatures, again due to the backpressure, can also cause the oil within the CHRA to carbonise. Often misdiagnosed as insufficient lubrication or oil contamination, this causes premature wear to the shaft, thrust plate, seals, and bearings and restrictions in the feed lines.
- Carbon build up in the turbine side piston ring(s), piston ring grooves, oil flinger groove and nozzle ring, preventing effective oil control.
- Over time, the excessive heat inside the turbine housing can cause the turbine wheel to fail from high cycle fatigue.

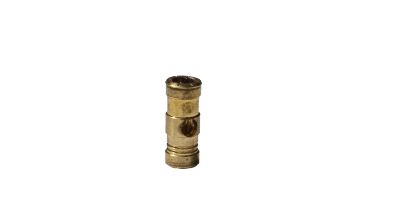

How to prevent DPF related turbo failures?
Although it can take some time for a DPF to block, once this happens, turbo failure can occur very quickly. Therefore, it’s always advisable to follow some simple measures when replacing or refitting a turbo:
- always check the vehicle’s DPF – if the soot levels are high enough to stop the DPF from regenerating on its own, a forced regeneration, usually via a diagnostic scan tool, may be required.
- if the blockage is severe, the only way to completely remove the particles is to either fit a new OE-quality filter, or have it professionally cleaned by a company like Carwood.
- encourage your customer to drive for 30 minutes or so, at speeds over 50mph, every few hundred miles – this will allow the exhaust temperature to get hot enough to burn off any excess soot
- use manufacturer approved engine oil – this is designed to produce as little diesel particulate material as possible.
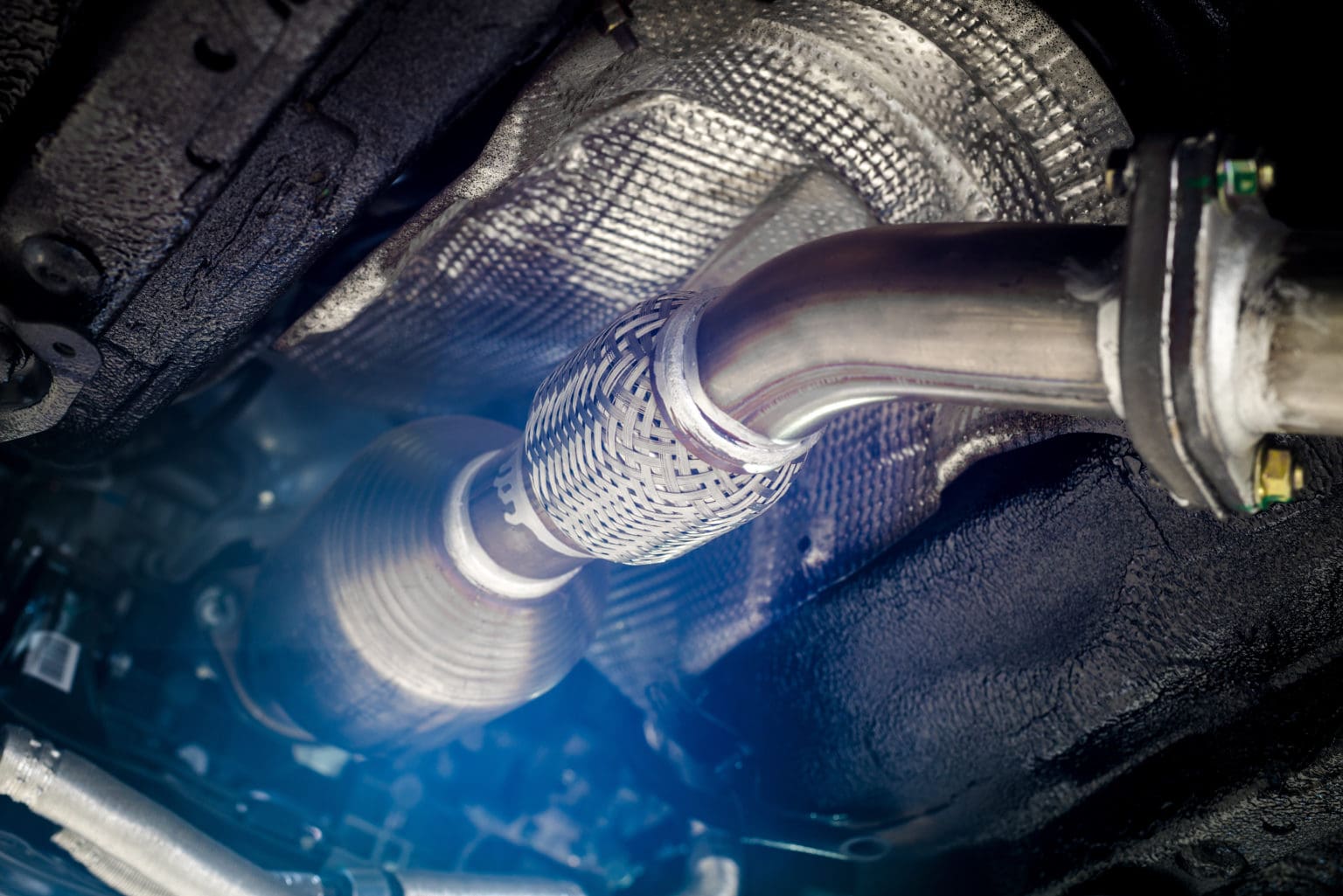
How to resolve a DPF related failure?
- remove the DPF and have it professionally cleaned off-vehicle
- thoroughly check and clean the entire exhaust system – replace components as required
- fit new oil feed and return pipes whenever installing a turbo
- check and clean the intercooler and pipes – replace if needed
Whilst this may add additional expense to your customer’s bill, it is far more cost and time-effective than having to fit another turbo, and potentially an engine, when they return with the same issue soon after. So, remember to always diagnose and fix what caused the original unit to fail, before fitting a new turbo.