Why oil feed pipes fail?
The position of the feed pipe within the engine bay means they are particularly vulnerable to damage from heat and other issues such as:
- Material wear: over time, the continued high heat from the engine, can damage the pipe and break down the materials, especially the rubber
- Carbon deposits: the excessive temperatures can also cause deposits of carbonised oil to form in the pipe’s inner walls, limiting the flow of oil to the turbocharger
- Contamination: even the smallest particles of dirt, soot, fuel water or abrasives can collect in the pipe restricting flow
- Kinked lines: flexible oil lines can easily be twisted or bent during installation, causing a build-up of oil pressure, and leaks from both the turbine and compressor ends
- Worn o-rings: many feed pipes use o-rings to seal the mounting locations. Over time, they can dry out and become brittle, leading to oil seeps and leaks
- Damaged connectors: during removal and refit the connectors can be damaged, meaning that the entire system is no longer adequately sealed
- Liquid sealant: although it should never be used it in the air or oil system, liquid sealant can easily become detached and block oil passages – it can also harden and break off into the turbo’s rotating assembly.
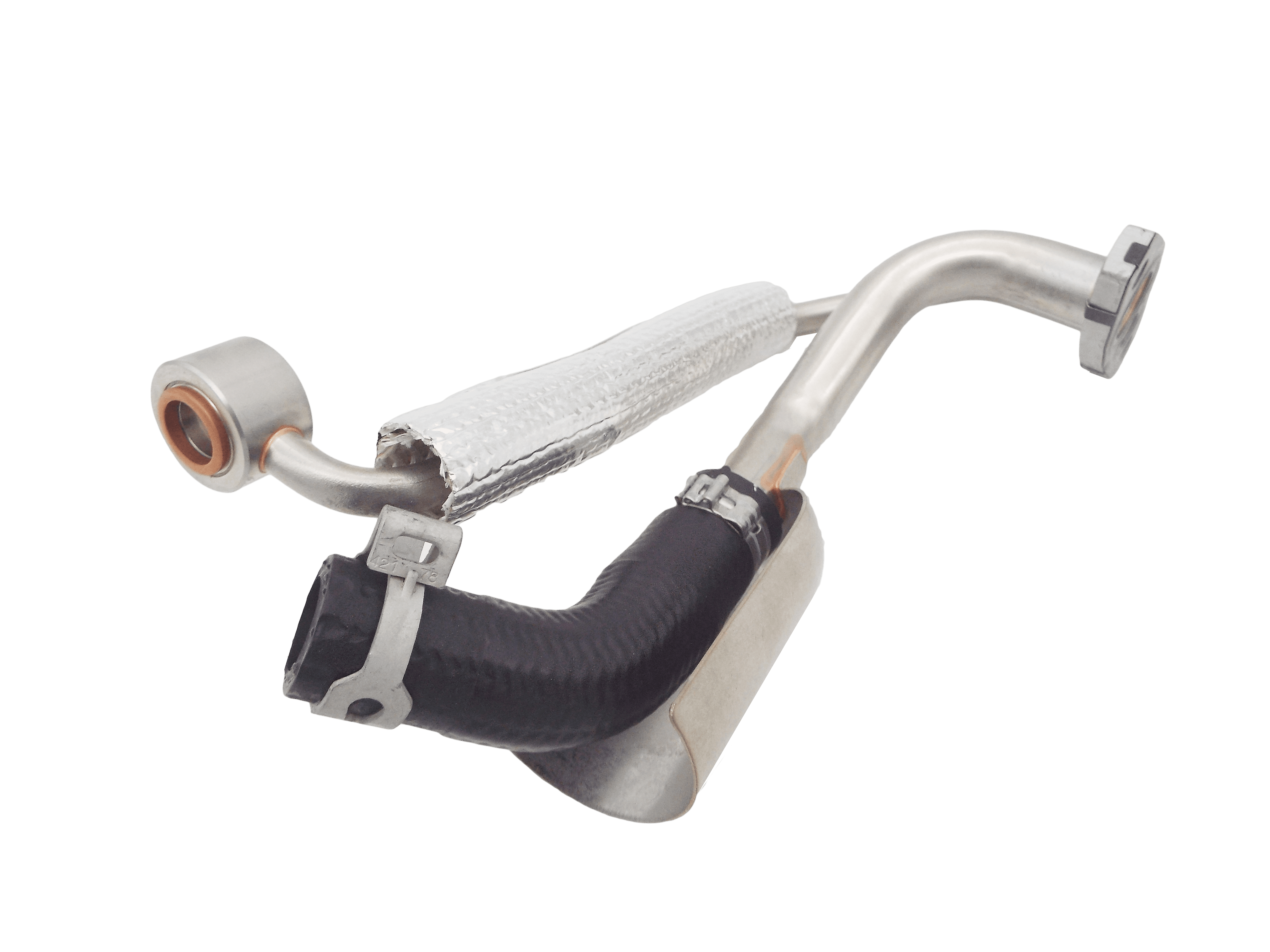
Some vehicles are more prone to issues than others. For example, PSA 1.4 and 1.6 litre HDI engines are known to suffer from extensive carbon build-up and is why technicians should ensure the entire oil circuit is checked, thoroughly cleaned and key components such as the oil, oil filter etc are changed, along with the feed pipe, when fitting a new turbo. Other applications that are susceptible to problems include Ford Transit/Land Rover 2.2, 2.4, 2.5 LD, Vauxhall Astra, Meriva, Insignia, Zafira A14 NEL/NET, Saab 9-3, 9-5 2.0 and 2.3 Turbo and Audi A4 and VW Passat 1.8T.
What to look out for in faulty oil feed pipes?
Given the critical role that the feed pipe plays, it’s a good idea to inspect it on a regular basis for signs of wear and tear. Spotting potential problems early on, will help minimise the possibility of future damage to the turbo and even the engine:
- Cracked rubber: one of the most obvious signs that there’s an issue, is cracking to the rubber from prolonged exposure to the temperatures in the engine bay – if left unchecked this will cause much bigger issues
- Bulging spots: another common sign is bulging spots in the hose, again due to the heat, as well as the constant flow of pressure through the pipe – eventually the spots will tear, causing the oil to leak out
- Oil leaks: noticeable puddles of oil underneath the car are also a sign that the pipe is damaged, which big or small, can lead to catastrophic and premature failure of the turbo
When should feed pipes be replaced?
If you, or your customers spot any of these issues, then the pipe is almost certainly faulty and should be quickly replaced. However, it is also advisable to fit a new one every time a turbo is installed, since even a momentary restriction in the supply of oil, due to a blockage in the pipe, or a leak, can cause severe damage to the turbo and potentially the engine. Although a new pipe may add a few pounds to the bill, it is much more cost effective then having to refit a whole new turbo, saving you and your customers valuable time and money in the long run. As well as ensuring a high-quality, long-lasting vehicle repair.
Installation tips
For a best-practice turbo service, it’s important to follow some simple steps when fitting a new oil feed pipe.
- keep the pipe in its protective bag until its ready to be installed
- before fitting, lubricate the turbocharger inlet with a small amount of oil to protect the turbo and prevent it from turning dry after the first start
- use new washers and screws, as appropriate
- use the intermediate supports or fasteners, where necessary, to avoid fatigue failures – pay attention to the disassembled pipe for the correct positioning
- never bend the pipe or use excessive force – feed pipes for PSA 1.4 and 1.6 litre HDI engines, for example, feature o-rings housed in mobile connectors at either end – any force could damage the inner o-ring and sealing
- ensure the pipe is correctly torqued at both ends, as per VM guidelines.