What is overheating?
Extreme heat can destroy many things. And the same goes for turbochargers. Whilst they are designed to withstand exceptionally high temperatures, prolonged exposure to 1,000°C plus, and/or cooling issues, will eventually take its toll on the turbine side of the turbo. This can contribute to a whole host of problems, which, if left unchecked, can cause severe damage to other components, and even complete turbo failure.
What are the causes of overheating?
There are a number of issues that can cause the turbo to get hotter than expected:
- poor quality oil, or the incorrect grade, will not provide sufficient lubrication or protection against heat and friction
- low, degraded and/or incorrect grade of coolant or antifreeze levels will similarly hinder heat transfer and component protection
- damage to, or blockages in the coolant system
- non-dealer remapping, engine modifications or fitting a standard turbo to a remapped engine can push the engine and turbo beyond its operating limits
- repeated hot engine shutdowns causing residual oil in the turbo’s bearing housing to carbonise – over time, this can cause accelerated wear to internal components
- damaged or blocked exhaust system components, such as the DPF, leading to excessive exhaust gas back pressure and heat
- obstructed oil drain line or damaged crankcase,
- restricting the flow of oil out of the turbo, preventing it from cooling
restrictions to the air flow such as a blocked filter, a faulty MAF or MAP sensor or damaged air intake pipe, resulting in insufficient air to cool the engine - coked oil feed and return lines restricting the supply to and flow out of the turbo
- faulty or leaking injectors causing the engine to overcompensate for changes to the air fuel ratio
What are the signs of overheating?
As well as the common signs of turbo failure, there are some clear indicators that the turbo is either operating beyond its maximum rated temperature or is not being properly cooled. These include:
- check engine light illuminated
- a smoky exhaust
- loss of power and performance
- abnormally loud whirring noises
- lack of boost, or drop in pressure, if the vehicle is fitted with a boost gauge
- discolouration that extends from the turbine wheel base and along the shaft from the head
- staining to the turbine shaft journal surfaces caused by heat soak (hot shutdowns)
- discolouration of internal components such as the thrust washer and flinger
- deposits of carbonised oil on the turbine shaft condensed on the piston ring, piston ring groove and oil flinger groove
- glazing to the turbine end of the turbine shaft
- carbon deposits in the oil feed and return lines
- excessive wear to and corrosion of turbocharger bearings
- deformation of the turbine and compressor wheels and housing
- damage to turbine blades including stress cracks, wear to the tips and/or partial loss of blades
- blue discolouration to the shaft at the turbine end of the turbo
How to prevent overheating?
By adopting some routine maintenance procedures, the turbo can be protected from excessive temperatures:
- perform regular oil and oil filter changes and keep the vehicle topped up with the correct grade of oil, as per manufacturer guidelines
- check the coolant levels and top up if necessary, with the right grade for the driving conditions – remember to only remove the filler cap on a cold engine to avoid the risk of scalding
- inspect the coolant system for signs of wear to hosing, damage to radiator etc – clean and/or replace as necessary
- check the entire air induction system for restrictions including the air filter, MAF sensor, MAP sensor and pipework – fit new air filters and replace other components as needed
- fit new oil feed and return pipes when replacing or refitting a turbo
- inspect the exhaust system for any leaks and blockages to the DPF, catalytic converter etc – clean and replace, where relevant
- following a long or hard drive, allow the engine to run at idle for 1-2 minutes before switching off the engine to ensure the turbo is sufficiently cool
- avoid non-approved chipping or over-fuelling – any engine modifications should be performed by a specialist
- ensure you only ever fit the right turbo for the application
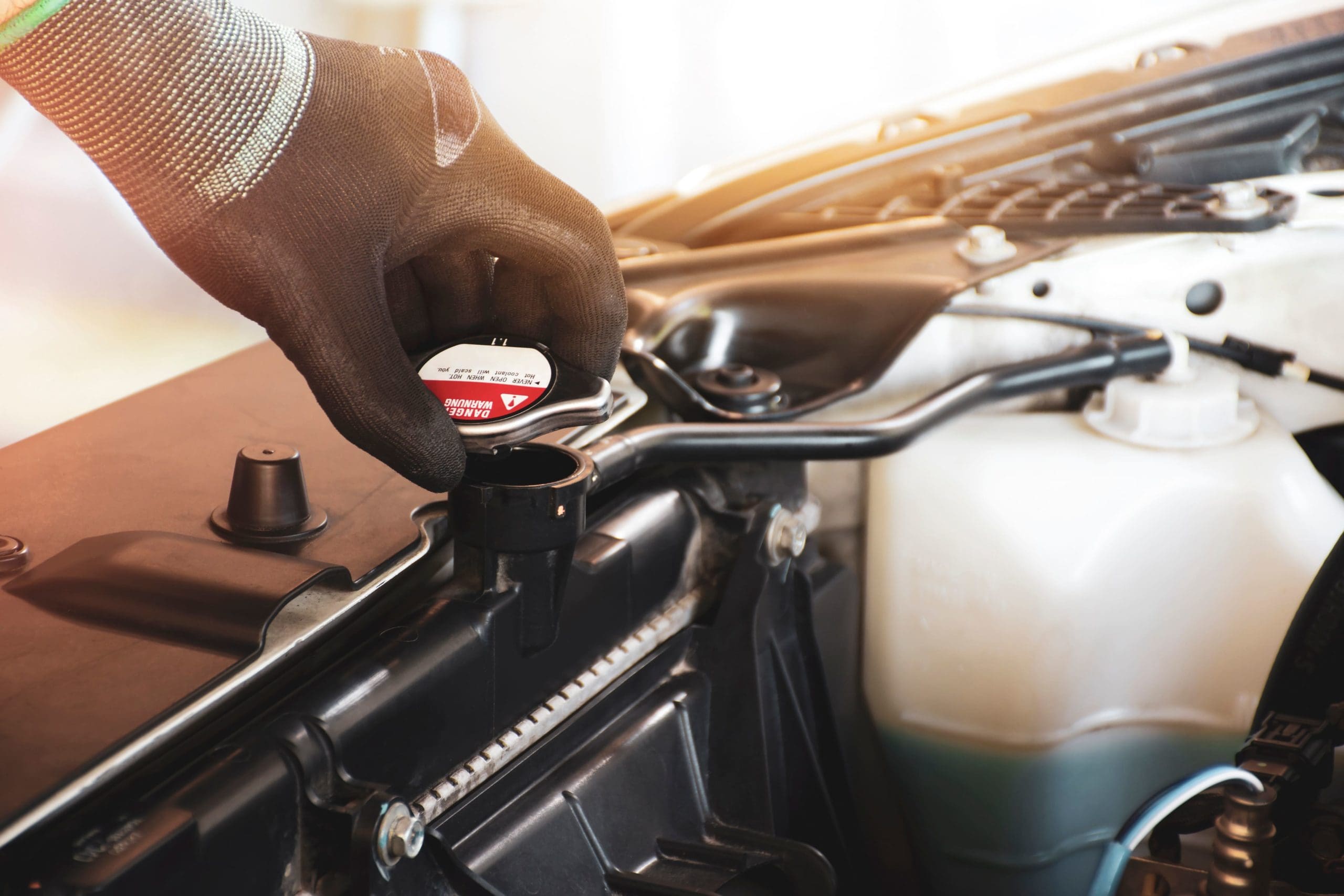
How to resolve turbo failure caused by overheating?
If a failure due to overheating is confirmed, it’s important to address and fix the root cause, before replacing the turbocharger. Remedial actions should include:
- conduct an oil system flush following VM guidelines
- fill with the correct grade and quantity of oil
- fit new OE-quality oil and air filters
- complete in-driving exhaust self-cleaning cycles, if available
- check the coolant system and replace components, as necessary
- top up coolant with the correct grade and quantity
- check the air induction system and replace components, where needed
Whilst this may add additional expense to your customer’s bill, it is far more cost and time-effective than having to fit another turbo, and potentially an engine, when they return with the same issue soon after. So, remember to always diagnose and fix what caused the original unit to fail, before fitting a new turbo.